Die Projektidee
Viele kennen das Problem: Man will eben mal schnell Nudeln kochen, findet sich aber in einer Küche mit einem altertümlichem Massekochfeld wieder, welches zum Aufwärmen das Wasssers eine halbe Ewigkeit bracht.
Als der Paul Award Ende 2019 durch den FED, dem Fachverband für Design, Leiterplatten- & Elektronikfertigung in Zusammenarbeit mit der Fachzeitschrift “Elektronik Neo” ausgeschrieben wurde, nahm ich mir diese Problemstellung als Thema für meine Projekteinreichung. Ich bennante das Projekt “TemperatUHR”, damit gleich der Zusammenhang zwischen der Temperatur und der Zeitkomponente hergestellt wird. Mein Projektziel war es, die Problematik des langen Wartens auf Temperaturveränderungen von Flüssigkeiten (und theoretisch Gasen, diese ändern aber in der Regel schneller ihre Temperatur) durch eine kleine Messstation und einer dazugehörigen App zu lösen.
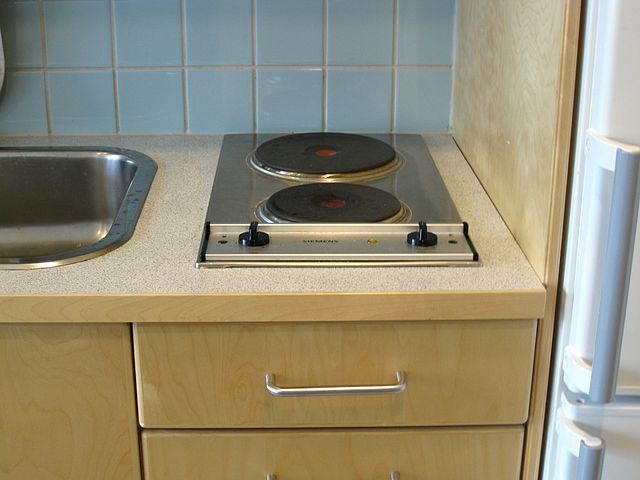
Die Entwicklung der "TemperatUHR": Hardware
Da eins der Ziele des Wettbewerbs es war, eine Leiterplatte zu entwickeln, war diese Thematik eine der ersten Aufgaben für mich: Nachdem ich mit einem Arduino Mega 2560 die Funktion des Temperatursensors (ein hochgenauer DS18B20 12-Bit Sensor mit niedrigem Stromverbauch) erfolgreich testete, begann ich, eine Leiterplatte zu entwerfen. Diese sollte klein und einfach zu produzieren sein. Mein ursprünglicher Plan war es, die Leiterplatten im RaumZeitLabor in Mannheim zu entwickeln, diesen Plan musste ich aber aufgrund von Material- und Qualitätsproblemen verwerfen.
Doch bevor ich mit dem Design der Leiterplatte beginnen konnte, musste erstmal ein Schaltplan erstellt werden:
Nachdem der Schaltplan stand, wurde es dann tatsächlich Zeit für das Leiterplatten-Design:
Auf nur 55 mm * 40 mm brachte ich die gesamte Ladeelektronik, den Microcontroller, alle Vorwiderstände, einen USB-Anschluss sowie Pin-Header zum Abgreifen der LED-Spannungen und der Ein-Ausschalt-Verbindung unter. Ich verzichtete größtenteils auf SMD-Komponenten, damit auch Personen ohne große Löterfahrung das Projekt einfach nachbauen könnten. Damit waren die Toleranzen jedoch so gering, dass eine eigene Anfertigung praktisch unmöglich wurde. Deshalb sendete ich die Gerber-Dateien an einen Leiterplatten-Prototoypenhersteller, damit die PCBs (inkl. Lötmaske) richtig hergestellt werden konnten.
Acht Tage später klingelte der Postbote und brachte ein Paket mit 10 der Leiterplatten vorbei.
Also ging es ans auflöten der Komponenten auf die Leiterplatte, wie immer beginnend mit den kleinsten Komponenten bis hoch zu dem großen Hauptprozessor:
Als die erste Leiterplatte fertig zusammengebaut war, ging es damit endlich an die
Software-Entwicklung
Zuerst war die Frage zu klären, welche Programmiersprachen ich für das Projekt nutzen wollte. Ich begann als Test, eine App in Apples nativer Programmiersprache Swift zu entwickeln.
Nebenbei probierte ich SwiftUI als Userinterface-Design-Tool aus, jedoch begrub ich die Idee der nativen Swift-Applikation, nachdem die Limits von Apples Stromsparfunktionen in iOS nicht alle geplanten Funktionen der App zugelassen hätten. Deshalb schaute ich mich nach Alternativen zur Smartphone-Kommunikation mit Microcontrollern um und wurde schlussendlich bei der IOT-Plattform “Blynk” fündig: Die (für den Anwendungszweck kostenlose) Plattform hatte als große Pluspunkte eine Geräteübergreifende Kompatibilität, sodass ich nicht nach der Swift-App noch in Java eine Android-App hätte entwickeln müssen. Zudem war die Anbindung an einen Microcontroller simpel und übersichtlich gestaltet. So begann ich, parallel in Blynk für’s Smartphone und in C++ für den Microcontroller die Software zu entwickeln. Insgesamt rund 400 Zeilen Code waren auf der Microcontroller-Seite ausreichend, um die App-Anbindung zu realisieren. Neben der App-Anbindung wurde noch eine Over-The-Air (OTA) Updatefunktion integriert, damit die Sensoreinheit ohne Gehäuseöffnung neue Software aufgespielt bekommen könnte.
Nachdem die Kommunikation zwischen Microcontroller und der App zuverlässig funktionierte, stand ein letzter Schritt auf Projektseite an, damit die Entwicklung abgeschlossen war:
Der finale Zusammenbau
Um das Projekt zu vollenden, wurde es Zeit, ein Geäuse für das Projekt zu erarbeiten: Mit den Maßen der Batterie, der Leiterplatte, der LED und des Anschalters zeichnete ich in der CAD-Software Fusion360 ein passendes Gehäuse, welches ich an einem 3D-Drucker aus PLA ausdruckte. Um die Elektronik vor Vibrationen zu schützen, kleidete ich die Unterseite noch zusätzlich mit einem synthetischem Stoff aus.
Danach legte ich erst die Batterie und dann die Leiterplatte, in das Gehäuse. Die Leiterplatte wurde zusätzlich mit einem Klebstoff in dem ausgekleidetem Gehäuse befestigt.
Das Endergebnis
Preisgekrönt wurde das Projekt Ende November 2020 bei der Abschlussveranstaltung, nachdem diese Aufgrund der Corona-Pandemie mehrmals verschoben werden musste. Die Abschlussveranstaltung Ende Novemeber wurde dann digital durchgeführt, neben den Teilnehmer*innen des Projektes war die gesamte Jury dabei. Das Projekt erhielt den ersten Preis für die exzellente Nachbaubarkeit, ein gutes Konzept und eine vollständige Projektdokumentation. Zudem wurde der Open-Source-Aspekt des Projektes lobend hervorgehoben.
Im Rahmen der Preisverleihung wurde eine Pressemitteilung vom FED veröffentlicht:
Für die Abschlussveranstaltung des Wettbewerbs produzierte ich zudem ein Video, welches das Projekt kurz erklärt:
Dankesagung
Abschließend will ich dem FED und den Sponsoren des Wettbewerbs für die Organistation und Finanzierung der Veranstaltung danken. Der Wetttbewerb bietet dem Elektrotechnik-Nachwuchs eine seltene Chance, Projekte öffentlich darzustellen und an den eigenen Fähigkeiten zu arbeiten.
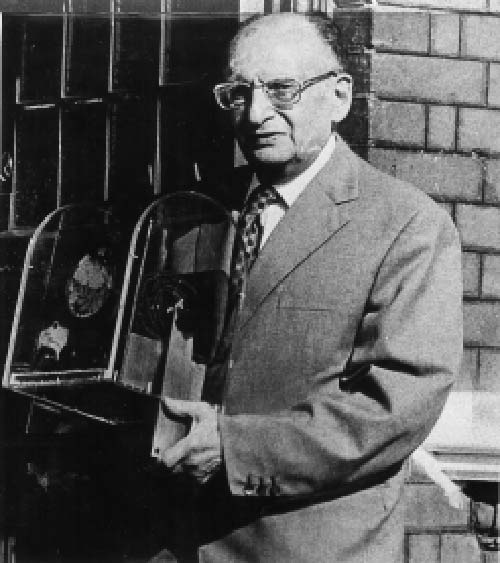
Hintergrund: Der PAUL Award
Der erste PAUL Award wurde 2019 vom FED e.V., dem Fachverband für Design, Leiterplatten- & Elektronikfertigung, ausgeschrieben. Kooperationspartner war dabei die Fachzeitschrift Elekronik Neo, Sponsoren unter anderem Viscom und Technosert Electronic.
Der Branchenpreis für junge Elektronikfans richtete sich an Schüler, Studenten und Berufsanfänger zwischen 15 und 25 Jahren die Freude an der Elektrotechnik und Elektronik haben. Es traten insgesamt 19 verschiedene Teams und Einzelkämpfer aus dem deutschsprachigen Raum gegeneinander an. Eine Jury bewerte die eingereichten Projektergebnisse anhand Bewertungskriterien wie Kreativität, technisches Verständnis oder Qualität des Projektergebnisses und ermittelte drei Sieger.
Bennant wurde der Preis nach Paul Eisler, einem österreichischem Ingenieur und dem Erfinder der Leiterplatte, der nächste PAUL Award wird am 21. Januar 2021 ausgeschrieben.
3 Current Opinions